Raising layers on an industrial scale may be challenging at times, but producing specific pathogen free (SPF) eggs for vaccine production takes the level of difficulty to a whole new level.
Few understand the risks and rewards better than Somboon Sinpatanasakul, founder and managing director of Thai SPF.

Somboon Sinpattanasakul (right) and Chirawat Kerdpanich pose with a photo depicting the late King Bhumiphol’s call
to “attach gold leaf behind the Buddha image,” which means that people should do good deeds humbly and discreetly
Even though he had no experience with SPF egg production, Mr Somboon took on the task in part due to a sense of civic duty.
The Thai government’s National Agenda states that developing capacity to produce quadrivalent influenza vaccine for domestic use and to assist other countries in the region is an urgent priority for establishing the Kingdom’s last line of defence in the event of a u pandemic.
Mr Somboon was inspired by an article published by the National Vaccine Institute stating the necessity of developing local capacity to manufacture influenza vaccine in an emergency situation.
A microbiologist by training, Mr Somboon said the rationale behind the project is not pro t driven, but rather a matter of health security for all Thais and their neighbours.
He cited the outbreak of infuenza H1N1 u in 2009 as a wake up call.
At that time, flu vaccines were scarce and not accessible to everyone, even the rich and well-connected. Imports were the only option, and supplies were delivered too little, too late.
“People’s lives are precious and that comes first. If return on investment was the top priority, the project would never have taken off. Capital is not an issue. We can always raise capital along the way,” he said.
By having its own SPF farm, Thailand will avoid supply bottlenecks by becoming self-sufficient in biological materials needed to mount an effective defence against an outbreak of pandemic flu.
Relying solely on offshore sources is fraught with risks. Imported SPF eggs from Europe or the United States cost around 300 baht apiece. Buyers are obliged to sign a purchase agreement 8-10 months prior to shipment, but in the event of a full-blown pandemic, no supplier can guarantee delivery.
Obviously, all countries look after their own people first, and in a genuine crisis any purchase agreement wouldn’t be worth the paper it was written on.
Apart from Thai SPF, Thailand’s DLD also supplies SPF eggs for producing around 900 million doses of animal vaccines a year. DLD’s operation can be switched to manufacture human vaccines in case of an emergency.
According to the Ministry of Public Health, the country needs around 60-65 million SPF eggs/year to meet annual vaccine demand.
In addition to the flu vaccine, the company is supplying SPF eggs for NSTDA to do new research against dengue fever.
Soft loans and grants from the World Health Organization helped expedite the project. The WHO has urged Thailand to serve as a regional hub to supply vaccines for seasonal in fluenza and bird flu.
Thai SPF’s egg output will remain in a holding pattern until an influenza vaccine facility located in Kaeng Khoi, Saraburi, operated by Thailand’s Government Pharmaceutical Organization (GPO), is finished. The plant is under construction with the first batch of vaccines due in 2020. At that time, GPO will become the largest buyer of SPF eggs, he said.
Risk assessment
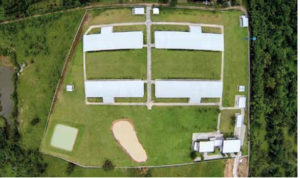
Aerial view of all four SPF poultry houses
Building a farm where nothing can ever be allowed to go wrong is no easy feat. Mr Somboon’s SPF operation began with a thoroughly conducted risk assessment. The farm has been built on an artificial plateau elevated 1-5 meters above ground to prevent flooding and enclosed with hills as a natural border.
A large piece of land in front of the farm was purchased as a buffer area to maintain plenty of space from nearby communities.
As a further measure to maintain continuity of operations, Thai SPF is looking for an additional site to preserve a backup supply of its precious seed stock so that SPF flock propagation can be restarted promptly if, for example, a fire breaks out and destroys all the birds.
A cold start
Farm construction and site development commenced in 2012. The construction process was not smooth, even though the project was a matter of national security. Surrounding communities feared that the SPF farm could affect their quality of life with odour, noise, dust and create an industrial blight on the landscape.
After numerous lawsuits and testimonies by experts from various public health agencies explaining the necessity of having a local SPF farm, the court finally granted Thai SPF permission to continue construction.
To prevent future conflicts, the company later decided to buy additional land as a buffer against expansion by the nearby community.
The main reason raising SPF hens is so difficult is the fact that they must be free of contagious poultry diseases which are transferable from parents to offspring for at least three generations. Thai SPF’s first batch of eggs were brought in from North America and hatched in 2015. The first SPF eggs were harvested the same year.
However, an outbreak of avian influenza H5N2 in the United States that closed the door on further imports of SPF seed stock convinced Mr Somboon of the need to develop breeding stock internally.
Flock replacement is problematic because non-SPF birds can’t be added to the flock.

SPF ock
Blood specimen shipments to North America and Europe are totally banned. Instead, the company has arranged with the Faculty of Medical Technology at Mahidol University to perform immune testing in line with USDA and EU guidelines that require all birds to be tested for 31 avian diseases.
EU Pharmacopoeia certification has stalled now that imports of live antigens to Thailand have been suspended following the bird flu outbreak.
The outbreak forced Mr Somboon to seek a new SPF breeding stock supplier. Eventually, he contacted a specialist in the US with intensive vaccine egg production experience. He booked a flight and rented a car. With Google maps as his guide, he drove across the country to meet with him in person.
After learning about his objectives and Thai SPF’s current operations, the expert openly questioned Mr Somboon’s sanity, wondering why anyone would take up such a delicate operation without any prior experience in poultry farming.
Finally, Mr Somboon managed to convince his new friend to help him with fine tuning management and selecting breeder lines.
Production

oultry house (17mx72mx4m) stocks six birds/sq m. The company uses a brood-grow-
lay production system with single age all-in all-out.
The first phase contains four houses in total, located on a 6.4-hectare secluded area. To call the operation’s biosecurity “rigorous” is surely an under-statement. The office and preparation activities are situated in front of the farm. Workers have to shower twice before entering the rearing area.
The birds are beak trimmed in the first week. They are reared on slatted floors, rearing density six birds/sq m. The four houses (17mx72mx4m) are capable of supplying around 1.5 million SPF eggs/year at full capacity.
The birds are neither vaccinated nor treated with antibiotics. Males and females are reared together. Mortality from week 17 through to the end of production at week 70 is below 0.1% per week.
Keeping the birds free of exotic animal pathogens is critical for producing human vaccines. For example, the birds must be free of avian in fluenza, mycoplasma, salmonella, chicken anemia virus (CAV) and avian leukosis virus.
All birds are tested at least once for the range of pathogens listed in the European Pharmacopoeia either at point of lay or by 20 weeks of age.
After that, 5% of the flock has to undergo testing on a monthly basis. Every fortnight, 2.5% of the flock is randomly picked for testing to reach the 5% monthly testing requirement.
The hens are in service for 70 weeks, starting from day-old chicks. After depletion some are donated to schools and universities and the remaining birds are sold to traders for processing. The average bird yields 312 eggs in total.
Each house contains a small office area, a single-stage setter and hatcher holding 14,400 eggs, water treatment devices, and an air handling unit (AHU) for air purification.
Water and air quality

A hopper feeder automatically replenishes feed in the feeder lines. Feed is delivered in 30 kg bags. Each bag is double wrapped. The outer layers are cleaned with chlorine dioxide and moved to
a warehouse in each barn and then fumigated. Feed bags are then torn open and loaded into
a hopper bin.
Water is drawn from an artesian well, filtered with resin and manganese, treated with chlorine dioxide and then stored in a central stainless steel tank. The water is then pumped to each house.
The water is filtered again and stored in separate tanks before use. It is tested for chlorine dioxide concentration every morning and water samples are taken for bacteria culture. Also, water used for the cooling pads has to be cleaned and disinfected with chlorine dioxide.
The AHU is fitted with pre-filters, medium filters and HEPA filters capable of removing 99.97% of airborne particles greater than 0.3 mm in diameter. Inside the poultry house, positive air pressure at 0.3-0.4 inch of water is maintained.
Each house is fitted with sensors at the front, mid and rear to monitor temperature and humidity.
There are two AHUs fitted for each house. One is designated as a backup in an emergency situation.
Manure is removed at least twice a week to reduce ammonia accumulation.
The birds are fed a vegetarian diet. Thai SPF sends its own feed truck to pick up feed from a contracted feed mill to minimize cross-contamination risks.
“It is too complicated to trace the whereabouts of external feed trucks which could potentially serve as a vector through which disease could spread to the farm,” he said.
Biosecurity
Farm clothing is washed and dried within each unit. Four workers operate each house. They must have no contact with non-SPF poultry flocks, and must be finger scanned before entering their work areas.
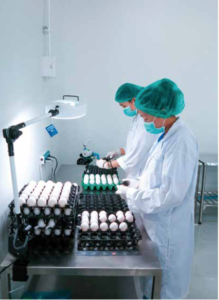
Eggs are meticulously selected. Of the
total harvest, around 80% are viable for use
They are required to take a shower when entering the farm area and take a second shower before entering the rearing area. Objects taken into the rearing areas must be disinfected.
Chlorine dioxide is the disinfectant of choice for air, water and surfaces. It is suitable for use with potable and drinking water because it is highly soluble, but not easily hydrolyzed. It remains a dissolved gas in solution.
Chlorine dioxide is a very strong oxidizer that effectively kills pathogenic microorganisms such as fungi, bacteria and viruses by disrupting their cell walls. It also prevents and removes biofilm and works well in hard water, said Mr Somboon.
Minimizing salmonella risk
Workers are obliged to take chest X-rays, blood, urine and stool tests to ensure they are in good health and to thwart salmonella infection. Dead birds and disposed eggs are incinerated because it is the most biologically safe method and does not attract rodents.
Viable eggs

Eggs are automatically collected via conveyor
Floor eggs are discarded. Only eggs collected from nests are used. Offspec eggs are those weighing under 48 grams, misshapen, cracked or with a misplaced air sac. The air sac should be situated at the top of the blunt end. Breakage due to handling is below 0.1%.
The eggs are either disinfected with or without water depending on customer requirements and delivered to an egg handling facility where they are subsequently taken for candling, cleaning and grading. The eggs are then moved to a storage room. Eggs produced the same day are stored together. Also, every viable egg has a ink jet printed code on its shell listing the flock number and production date for trace back.
The company also supplies 7-10 days old incubated eggs for customers who want to harvest embryo tissues at different growth stages for vaccine production. The hatching eggs are taken from the incubator for candling to sort out infertile and dead embryos.
The storage room maintains temperature between 14-18°C, relative humidity 75% to prevent weight loss. Eggs are stored for seven days at most.
Eggs are delivered to customers in an air conditioned van where the temperature is maintained at 18-23°C as per order. Cartons containing 360 eggs are disinfected with ozone to kill pathogens.